Logistics
How Using Your Phone for Mobile Barcode Scanning Drives Greater Accuracy in Logistics
While RFID readers have long been used for scanning items in the logistics and supply chain industry, modern disruptions lowered their rating on many points.
As online shopping booms, this technology struggles to handle the surge in orders. That explains why 56% of retailers face inaccurate inventory information, where even minor errors lead to poor order fulfillment, involving delayed deliveries, returns, higher costs, and dissatisfied customers. This problem continues to get worse when manual methods are still in use.
Thanks to the technological era we live in, this problem has a decent modern solution. Mobile barcode scanning came to replace their alternatives, offering greater accuracy in fulfillment operations and decreasing costs across your logistics ecosystem.
Wondering how?
Today's customers have high expectations for modern retailers expecting real-time visibility, and precise delivery time calculations. Such interactions set the tone for the overall service impression. Any misstep in this process could lead customers to quickly switch to a competitor offering swifter purchase experience.
If you find these scenarios familiar, it could be due to several factors:
- Your inventory data is scattered across disconnected systems, making timely data access challenging.
- Your logistics operations heavily rely on manual processes.
- You're dealing with outdated, internally developed legacy solutions that no longer keep up with modern demands.
Efficient inventory, delivery, and order management processes hinge on achieving accuracy, speed, and real-time tracking. Implementing mobile barcode scanning technology, which ranks as the third most adopted technology (51%) among 3PLs, helps meet these requirements easily.
Mobile barcode scanning is the driving force behind these improvements as it eliminates the inefficiencies of slow and error-prone manual inventory counting and data entry. Additionally, it offers such broader benefits as:
- Scanning products upon arrival in the warehouse and at critical stages during storage, retrieval, packing, and shipping;
- Accessing real-time information regarding the quantity and precise location of all in-stock items;
- Enhancing order picking and shipping accuracy, thereby reducing returns;
- Addressing a common challenge in the industry—staff training—by introducing digital strategies into the corporate environment;
- Utilizing generated datasets to measure various performance metrics and gain insights into warehouse operations' effectiveness.
Mobile Barcode Scanning in Logistics: Common Applications
Smartphones are readily available today, and paired with suitable mobile barcode scanning software, capturing and analyzing any image data is a piece of cake. Various mobile barcode scanning applications can help retailers shift away from dedicated barcode scanners and get valuable gains in several tasks.
End-to-End Mobile Barcode Scanning Inventory Management
Keeping track of every product and its properties in the warehouse is not easy. Mobile scanning, employing barcodes or QR codes, helps with this task. Products are tagged with unique identifiers, and mobile devices track all of them throughout the entire supply chain cycle.
From receiving new inventory to fulfilling customer orders, each step involves scanning. This ensures real-time inventory accuracy, minimizes errors in order fulfillment, and helps with demand forecasting to prevent overstocking or stockouts while optimizing inventory management.
Warehouse Management
In warehouse operations, barcode software for mobile scanning transforms how products are stored, located, and moved. Warehouse staff can scan barcodes, ensuring they pick the correct items for orders and reducing the time spent searching for needed products. Real-time data helps optimize warehouse space, ensuring efficient storage and preventing situations where products are past their expiry date but still occupy space in your warehouse.
Learn more about solutions to optimize your warehouse management in our full guide to 3PL warehouse management software.
Order Fulfillment Operations
Implementing barcode scans at each stage of fulfillment - from picking to packing and shipping - allows employees to verify the contents of each package before shipping it, reducing the chances of returns. In the event of a return, barcode scanning guides the re-stocking process, ensuring the item returns to its designated shelf promptly.
Last-mile delivery operations
Retailers share responsibility for delivering packages to the correct locations and meeting workflow demands. In turn, customers expect to receive their orders at the right place and time. This is where barcode scanning mobile phones come into play, ensuring that the last-mile delivery stage can adapt to meet these operational demands and customer expectations.
Delivery personnel and drivers use smartphones for various tasks. For instance, they can quickly identify the correct package by scanning QR codes on parcels with their phones. These devices also offer real-time updates, keeping drivers informed about any changes or essential information related to their deliveries.
Curious about last-mile delivery operations? Discover all the answers you need in our latest blog post: Last Mile Delivery: Concept, Challenges, and Making It Efficient
Contactless Proof of Delivery
As the pandemic hit hard in 2020, many 3PL companies started adopting mobile barcodes to replace the old practice of requiring physical signatures. This helped reduce millions of errors and created a digital record for each delivery.
The process looks simple: The package goes out for delivery with the delivery person, who has a mobile device equipped with a barcode scanner or a scanning app on their smartphone. When they reach the recipient's location, they use their mobile device to scan the package's barcode or QR code, which records the delivery time and location. The system confirms the successful delivery by associating the scan data with the recipient's information and the delivery record. The digital delivery record created serves as proof that the package reached the recipient as expected.
Let mobile barcode scanning be your solution to avoid inventory headaches, warehouse inefficiencies, and order fulfillment issues. Contact us to learn more about modern technologies for solving your logistics problems!
How Mobile Barcodes Drive Accuracy in Logistic Operations
Risks are a substantial part of logistics operations. Every movement, every shipment, and every step in the supply chain represents a chance to either optimize operations or introduce costly errors.
However, with the right tools and strategies, businesses can turn these risks into opportunities for improvement and growth. Here’s how mobile barcodes help reduce uncertainty and enhance accuracy in logistics operations:
Real-time Inventory Tracking
Mobile barcode scanners provide real-time tracking for inventory and operational activities way better than traditional handheld scanners. With each scan, the system updates the database immediately, providing accurate and up-to-the-minute information on stock levels, locations, and movements.
Moreover, when regular handheld scanners can't handle incomplete, crumpled, dense, or skewed barcodes, barcode-enabled software steps in to scan them without any problems, resulting in more accurate tracking with no missed scans.
Error Reduction via Barcode Verification
Mobile barcodes provide a fail-safe way to verify the information. Each item or package is assigned a unique barcode that contains essential details, such as product type, quantity, and destination. When these barcodes are scanned, it becomes nearly impossible to make mistakes in identifying, tracking, or shipping products.
For instance, if a warehouse worker scans the wrong item for an order, the system will immediately flag the error. This means fewer errors made by people, which saves money and keeps customers satisfied with a correct delivery. So, mobile barcodes ensure the right products reach their intended destinations with a high degree of accuracy.
Proper Categorization, Quick Order Location, and Product Retrieval
You can think of barcodes as labels for each product. These labels tell us exactly what each item is, making it easy to put similar items together. So, in big warehouses or distribution centers with tons of products, it's like having a map that shows exactly where everything is, or it’s like an organized library where each book has its specific spot on the shelf.
When an order comes in, workers can quickly find and pick the right items, similar to how a librarian quickly finds a book on request. This efficiency not only accelerates order processing but also substantially reduces the likelihood of shipping the wrong items to customers. Plus, you can never lose track of any crucial inventory item, ensuring that every order is both complete and accurate.
All of these elements come together to achieve three critical goals: precise product organization, faster order location, and rapid retrieval. This, in turn, boosts operational efficiency, ensures customer satisfaction, and significantly reduces errors.
Faster Returns Processing
Returns are a regular part of the logistics routine, and mobile barcodes simplify and speed up the often complex returns procedure.
When a customer wants to return something, you can just scan the barcodes on the returned items to verify if the item matches the initial records. This quick action will guarantee you accept only the correct products for restocking or replacement.
As a result, mobile barcodes streamline the returns process, allowing you to handle returns faster and with greater accuracy, ultimately leading to happier customers.
Reliable Package Labeling & Shipping
Mobile barcodes can also serve as a quality control system when it comes to labeling and shipping packages.
Here's how it operates: Each package receives a unique barcode or QR code containing essential shipment information, such as recipient details and tracking numbers, during the packaging process. At the shipping point, personnel armed with mobile barcode scanners scan these codes, creating the initial shipment record. The system then generates a shipping label with recipient info, method, etc., which is printed and attached to the package. The scanner validates that the shipping label matches the barcode on the package. If there's a mismatch, the system immediately flags it for resolution before the package proceeds for shipment.
Minimized Downtime
When data entry and tracking rely on manual processes, there's room for human error and delays. Barcode scanners, on the other hand, automate data capture and retrieval processes. This means fewer hiccups and less downtime.
Operations run without unnecessary delays or disruptions, all thanks to its ability to eliminate manual errors and tracking issues.
Compliance Assurance
In highly regulated industries like pharmaceuticals (e.g., FDA regulations in the United States) or food (e.g., HACCP standards), mobile barcodes help ensure compliance with strict quality and safety standards.
For example, you can monitor temperature-sensitive items, guaranteeing that products like vaccines or perishable foods remain within specified temperature ranges (complying with Good Distribution Practices, for instance). Each sensitive item gets a unique mobile barcode with product details, including its origin, destination, and handling requirements. Inside the packages, temperature sensors watch the temperature, and this data is linked to the barcode. As products move through the supply chain, personnel use barcode scanning mobile apps to scan the barcodes, which also triggers an alert if the temperature ever goes beyond the safe range.
This creates a clear record that proves compliance with industry standards, which can be shown to regulators when needed.
Data-Driven Insights & Real-time Analytics
Mobile barcodes generate a wealth of data that can be used to gain insights. This data includes details like when and where items are scanned, how long they spend in transit, and which routes they take. By analyzing this data in real time, businesses gain a clear picture of their operations.
For example, if certain products consistently encounter delays at a specific checkpoint, adjustments can be made to improve efficiency. Similarly, if demand for a particular product spikes in real time, inventory levels can be adjusted to meet this demand more effectively.
As a result, through real-time analytics, businesses can make informed decisions, fine-tune delivery routes, and adjust inventory levels based on actual demand.
Benefits of Mobile Barcode Scanning Software
The landscape of mobile barcode scanning solutions is vast, with various options available, each catering to specific needs and challenges. However, what they all have in common are the benefits they provide in terms of accuracy, speed, and cost savings.
- Inventory accuracy. So, barcode scanners will help you to know how much inventory you have or lack, alerting you each time when inventory falls below preset levels.
User-friendly barcode scanning mobile apps are accessible to employees at all levels. They simplify the process of capturing detailed product information and reporting damaged or missing items upon entry. Barcode scanners provide constant insights into your inventory levels and promptly alert you when they fall below predefined thresholds. - Cost savings. Operational, transportation, and warehousing costs in the logistics sector are skyrocketing, especially when it comes to fulfilling orders promptly and meeting the rising customer demand for same-day or next-day delivery.
Barcode scanning mobile phones are easily accessible to inventory managers, drivers, and various supply chain stakeholders. Mobile devices can perform multiple data capture to streamline everyday logistics tasks without missing a thing. - Efficiency gains. From receiving and warehousing to order picking and shipping, each step becomes more efficient and less prone to delays or mistakes with mobile barcode systems.
For example, barcodes help categorize products accurately for correct storage and quick retrieval. They also simplify the picking process by ensuring employees select the right items, which is especially helpful when dealing with similar products from different vendors. - Ability to adapt to growing demands. Upgrading traditional scanners can be challenging and expensive. In turn, mobile barcode scanning systems are adaptable and capable of handling fluctuations in volume and can be easily updated as per the demand of your logistic firm.
- Reduced margin for errors. In logistics, even minor errors can escalate to major problems. Mobile phones with barcode scanning capabilities minimize the margin for error by automating data entry and verification. It scans every product at each stage of the fulfillment process—picking, packing, and shipping, ensuring that the right items are in the right place at the right time.
- Multi-channel retailing. Developing companies sooner or later come to the point when they want to expand their reach on various platforms, for example, Amazon, Walmart, and Shopify. Using mobile barcodes is essential for them for two reasons.
Firstly, they help maintain accurate inventory levels across all platforms. When a sale is made on one platform, the barcode system updates the inventory count in real time, preventing overselling or understocking. This ensures that products are available when customers want them. Secondly, by efficiently managing inventory, companies can reliably meet demand on various platforms, reaching more customers and potentially increasing revenue.
No secret, it takes a lot of knowledge and experience to know how to code your own barcode scanning mobile application. A dedicated development team can help your company create a mobile barcode scanning solution based on its tech and industry expertise.
The ElifTech expertise in barcode scanning solutions covers the next aspects of logistics operations:
- Inventory management;
- Warehouse management;
- Order fulfillment;
- Last-mile delivery;
- Traceability and compliance;
- Contactless Proof of Delivery;
- Returns management;
- Asset tracking;
- Pick-up and drop-off services;
- Reporting and analytics
- …and your specific inquiry.
Explore our comprehensive solutions for managing warehouse & inventory, transportation, order/delivery, and reporting - all powered by cutting-edge barcode scanning technology. Set up a demo with ElifTech tech experts to see how your challenges can be resolved in action.
Conclusion
Barcode scanning technology has come a long way. Today, smaller mobile devices have taken the place of older, bulky, and wired scanners. It's a reminder that you don't need to make massive investments and postpone solving your challenges. Everything you need is now at your fingertips. By embracing these accessible mobile barcode scanning solutions, you not only enhance efficiency but also prepare for future changes, ensuring smoother and more competitive operations.
Browse our case studies and get actionable insights to drive your success
See more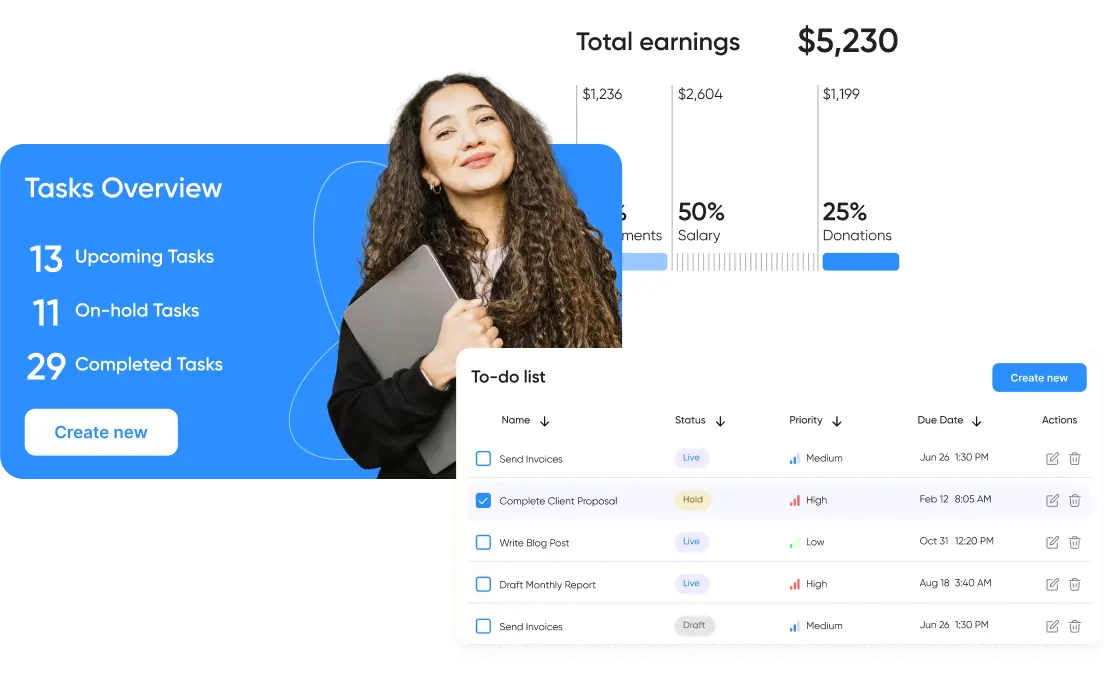